毕业设计(论文)材料成型及控制工程焊接方向毕业设计说明书
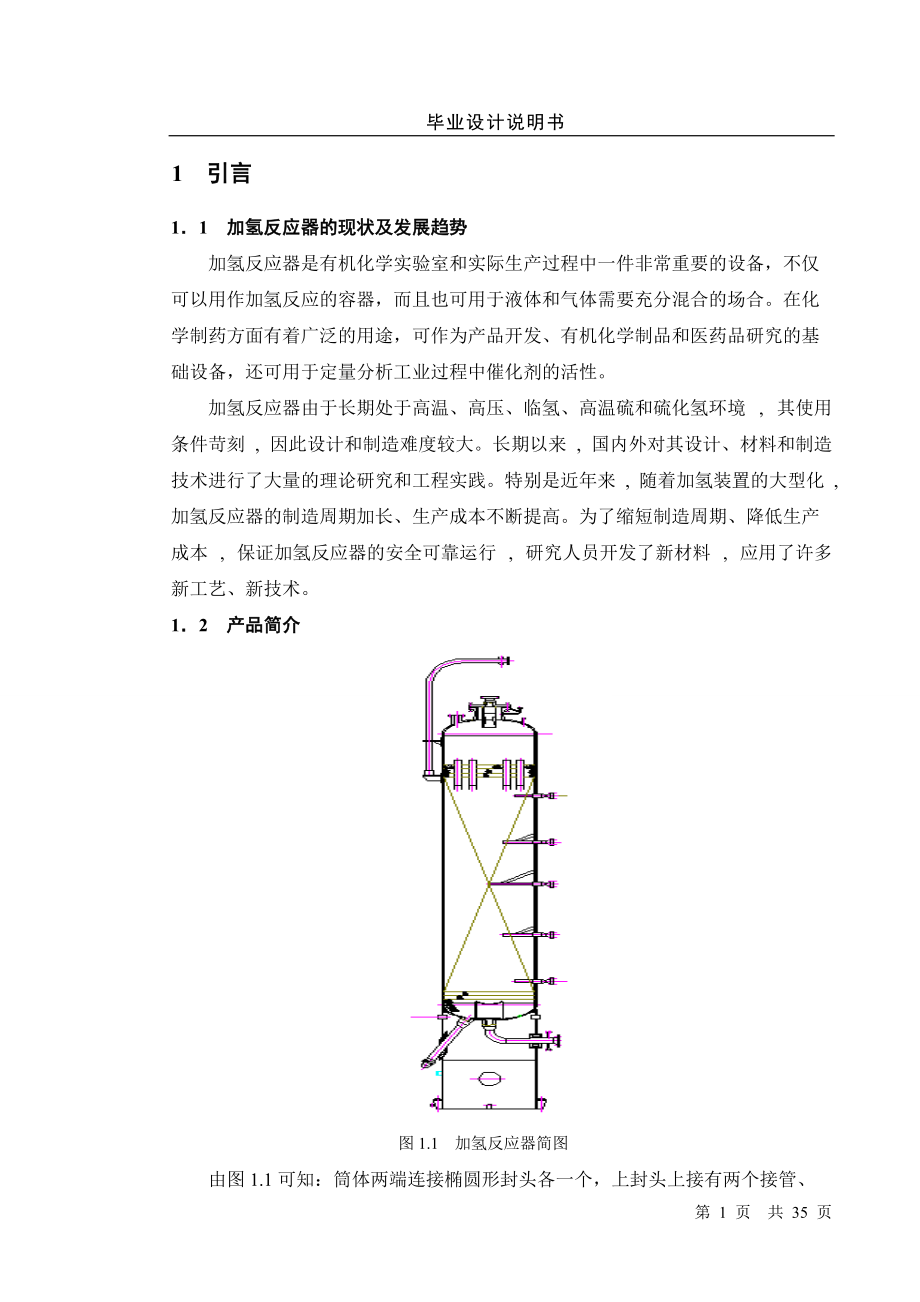


《毕业设计(论文)材料成型及控制工程焊接方向毕业设计说明书》由会员分享,可在线阅读,更多相关《毕业设计(论文)材料成型及控制工程焊接方向毕业设计说明书(35页珍藏版)》请在装配图网上搜索。
1、毕业设计说明书 1 引言 1.1 加氢反应器的现状及发展趋势 加氢反应器是有机化学实验室和实际生产过程中一件非常重要的设备,不仅可以用作加氢反应的容器,而且也可用于液体和气体需要充分混合的场合。在化学制药方面有着广泛的用途,可作为产品开发、有机化学制品和医药品研究的基础设备,还可用于定量分析工业过程中催化剂的活性。 加氢反应器由于长期处于高温、高压、临氢、高温硫和硫化氢环境 , 其使用条件苛刻 , 因此设计和制造难度较大。长期以来 , 国内外对其设计、材料和制造技术进行了大量的理论研究和工程实践。特别是近年来 , 随着加氢装置的大型化 , 加氢反应器的制造周期加长、生产成本不断提高
2、。为了缩短制造周期、降低生产成本 , 保证加氢反应器的安全可靠运行 , 研究人员开发了新材料 , 应用了许多新工艺、新技术。 1.2 产品简介 图1.1 加氢反应器简图 由图1.1可知:筒体两端连接椭圆形封头各一个,上封头上接有两个接管、一个法兰,下封头上接有卸料管、出口弯管,筒体内上部装有积垢篮,筒体上接有五个接管,筒体采用裙座支撑。 本次设计生产的设备为加氢反应器,属于三类压力容器,筒体直径1400mm,高13900mm,壁厚(16+3)mm,生产数量:两台设备。 筒体纵焊缝交错分布,避免了十字交叉,有利于减少焊接应力及变形;主要加工手段为焊接,此外还采用冲压、卷弯、机加
3、工等辅助工艺。 1.3 工艺性审查 加氢反应器技术特性见表1.1。 表1.1 技术特性表 设计压力(MpaG) 2.0 设计温度(℃) 400 工作压力(MpaG) 1.5 工作温度(℃) 370 物料名称 氢气、C1-C5烃、硫化氢 焊缝系数 1 腐蚀裕度(mm) 地震烈度 7 基本风压(N/) 400 保温厚度(mm) 190 保温重量(Kg) 最大容量(Kg) 最小重量(Kg) 全容积() 12.93 容器类别 三类 再生工作压力(MpaG) 0.15 再生工作温度(℃) 510 再生设计压力(Mpa
4、G) 0.3 再生设计温度(℃) 520 本设备按加氢反应器制造技术要求进行制造试验和验收。开口接管与壳体的焊缝表面应圆滑过渡。设备壳体上除工艺预焊件外不允许焊接设计以外的任何零件。捕集器(积垢篮)安装时,平面度允差3mm,其中心线与反应器同轴度允差3mm。卸催化剂前应拆除捕集器。容器的全部受压焊缝应进100%X射线探伤检查,射线探伤符合 JB/T 4730.2-2005《承压设备射线检测》规定中Ⅱ级合格。设备制造完毕后,以2MPa进行水压试验,合格后再以1.8MPa进行气密性试验。 经审查,该反应器设计合理,可以着手制定生产工艺。 2 焊接工艺分析 15CrMoR属于耐热钢,
5、焊前需要预热,预热温度150℃,焊后650~830℃退火处理。 0Cr18Ni10Ti属于奥氏体不锈钢,焊前不需要预热,焊后不需要热处理。 以上两种钢材均采用熔化极气体保护焊,保护气为Ar(99.9%)。优点如下:(1)焊接过程中电弧及熔池的加热熔化情况清晰可见,便于发现问题与及时调整,故焊接过程与焊缝质量易于控制。 (2)焊后不需要清渣,省掉了清渣的辅助工时,降低了焊接成本。 (3)生产效率高,易进行全位置焊及实现机械化和自动化。 根据某些具体情况,适当采用手工电弧焊施焊。 3 焊接生产方案的制定 1.方案的初步制定 方案一:制造出所用全部零件。零件组装成部件;封头、接
6、管、法兰、入口扩散器焊接成上封头组;筒体、筋板、接管、积垢篮焊接组成壳程;封头、出口收集器、出口弯管、卸料器焊接成下封头组;裙式壳体、接管、地脚螺栓座、接地板焊接组成裙式支座;裙式支座、下封头组、壳程、上封头组最后总装成加氢反应器。 方案二:制造出所用全部零件。零件组装成部件;封头、接管、法兰、入口扩散器焊接成上封头组;筒体、筋板、接管、积垢篮焊接组成壳程;封头、出口收集器、出口弯管、卸料器焊接成下封头组;裙式壳体、接管、地脚螺栓座、接地板焊接组成裙式支座;上封头组、壳程、下封头组卧装焊接组成反应器主体;反应器主体、裙式支座最后总装成加氢反应器。 2.方案分析 方案一:下封头组、壳程、
7、上封头组均采用吊装,增加了吊装工作量,但是容易实现装配 方案二:上封头组、壳程、下封头组卧装须特制装焊夹具,提高了成本。 3.制定方案 经上述分析方案一、二都可以实施。但考虑到方案二提高了成本而没有明显的优势,最终决定选用方案一。根据方案一制定出生产工艺流程图见图3.1所示。 图3.1 加氢反应器生产工艺流程图 4 生产前期准备 1.钢材复检 钢板复检:包括化学成分、各种力学性能、表面缺陷及外形尺寸(主要是厚度)的检验,采用抽检的方法,抽检率为20%。 钢管复检:内容包括钢管材质、圆度及型号,材料应具有质保书,标记齐全。 ①按批号复验化学成分。 ②同一种规格
8、的原材料,抽样进行晶间腐蚀倾向性试验。 ③凡需有特殊复验项目要求的还应按要求进行检验。 2.焊接材料的复检 对焊丝、焊剂等焊接材料的熔敷金属的化学成分、腐蚀、金相进行检查。经验收和复检合格后,焊接材料应放在符合管理要求的焊接库,并由保管人质在明显的位置作出材料标记。 5 主要零件的制造 5.1 法兰盖的制造 法兰盖形状及尺寸如图5.1所示。 图5.1 法兰盖简图 1、零件的主要技术要求 1)表面不得有裂纹及其它降低法兰盖强度和连接可靠性的缺陷。 2)螺栓孔中心圆直径和相邻两螺栓孔弦长允差为0.8mm,任意两螺栓孔弦长允差为1.6mm。 3)工件材料为15
9、CrMoR,锻件,级别为Ⅳ级。 2、工艺分析 根据工件材料性质和具体尺寸精度、粗糙度的要求,可以采用粗车的工艺来达到。 3、基准选择 以粗车后的小端外圆面和凸台端面为定位基准,在一次安装中加工大端各表面,以保证所要求的位置精度。 4、工艺过程 1)采用GB4235锯床,从φ250mm的圆钢上锯取长1840mm的一段,尺寸依据等体积法粗略算得,取加工余量10%。 2)始锻温度1150~1200℃,终锻温度800~850℃,使直径达φ9506mm,厚 度达1366mm。 3)滚圆修整。 4)垫环局部镦粗,始锻温度1150~1200℃,终锻温度800~850℃,使
10、凸台部 分厚度达666mm,直径达φ3006mm。 5)用凸模冲出φ249的通孔。 6)热处理,650~830℃退火,从而恢复组织。 7)粗车小端外圆和两端面至φ29057。 8)倒头粗车大端外圆和端面至φ940126,然后粗车出密封面凸台φ7496。 9)按图示要求车环槽。 10)划线,划出24个螺栓孔的线。 11)钻φ52的螺栓孔。 12)车外圆及孔口倒角。 13)按图纸要求检验。 其加工工艺参见附录A。 5.2 孔板的制造 孔板形状及尺寸见图5.2。 图5.2 孔板简图 1、零件的主要技术要求 1)表面不得有裂纹及其它降低孔板强
11、度和连接可靠性的缺陷。 2)工件材料为0Cr18Ni10Ti。 2、工艺分析 根据工件材料性质和具体尺寸精度、粗糙度的要求,可以采用粗加工的工艺来达到。 3、工艺过程 1)备厚度6mm的板料,划线划出φ259的圆。 2)气割割出孔板。 3)修整毛边。 4)在板上按图中要求划出19个φ44的孔。 5)钻孔φ44,修理各个孔边缘的毛边。 6)按图纸要求检验。 5.3 封头的制造 封头形状及尺寸如图5.3所示。 图5.3 封头简图 1、零件的主要技术要求 1)表面不得有裂纹及其它降低封头强度和连接可靠性的缺陷。 2)工件材料为15CrMoR+0Cr18
12、Ni10Ti。 2、工艺分析 根据工件材料性质和具体尺寸精度、粗糙度的要求,可以采用粗加工的工艺来达到。 3、基准选择 以中心线AB和CD为基准 4、工艺过程 封头由半个椭球和一个高度为h的圆柱形短节(封头直边部分)构成,其型式参数关系为: Di=4(H-h) DN=Di 封头外形尺寸如下: 公称直径:DN=1400mm 封头壁厚:δa=19mm 直边高度:h=50mm 封头总深度:H=400mm 封头制造工艺如下: 1)预处理:矫正,喷丸处理。 2)划线:椭圆形封头毛坯尺寸的计算为 式中: P—封头椭圆部分的半周长 a—椭圆的长半轴 b—椭圆
13、的短半轴 由于a=700mm,b=350mm,得出P=1715.9mm。 考虑加工余量后,封头毛坯直径可按下式计算: D0=P+2hk0+2S 式中:—封头冲击成形是的拉伸系数,取k0=1 S—封头边缘加工余量 h—直边高度 可求得D0=1835.9mm。 综上,在原材料上划一直径为1835.9mm的圆。 3)下料:采用等离子弧切割下料。 4)热冲压:先加热至1000℃,再水压机压制成形并预留直边加工余量。 5)二次划线:量取直边高度50mm划线,同时对所有孔划线。 6)切割:LGK8等离子弧切割机切出50mm直边。 7)制孔:按所划的孔线钻出φ20;钻中心孔φ50,
14、钻左边的孔φ50,然后分别对中心孔和左边的孔扩孔,分别扩至φ600,φ100。 8)修理毛边。 9)按图样要求检查其尺寸、质量等。 5.4 法兰的制造 法兰形状及尺寸如图5.4所示。 图5.4 法兰简图 1、零件的主要技术要求 1)表面不得有裂纹及其它降低法兰强度和连接可靠性的缺陷。 2)螺栓孔中心圆直径和相邻两螺栓孔弦长允差为0.6mm。 3)工件材料为15CrMoR,锻件,级别为III级。 2、工艺分析 根据工件材料性质和具体尺寸精度、粗糙度的要求,可以采用粗车的工艺来达到。 3、基准选择 以粗车后的小端外圆面和凸台端面为定位基准,在一次安装中加工大
15、端各表面,以保证所要求的位置精度。 4、工艺过程 1)采用GB4235锯床,从φ250mm的圆钢上锯取长435mm的一段,尺寸依据等体积法粗略算得,取加工余量10%。 2)始锻温度1150~1200℃,终锻温度800~850℃,使直径达φ5146mm,厚度达1036mm。 3)垫环局部镦粗,始锻温度1150~1200℃,终锻温度800~850℃,使法兰盖凸出部分厚度达686mm。 4)滚圆修整 5)用冲模冲φ249的通孔。 6)热处理,650~830℃回火,恢复组织。 7)粗车小端外圆和两端面,车出颈部,保证尺寸φ273、φ343、88。 8)倒头粗车大端外圆和
16、端面至φ51066.5。 9)粗车密封面φ3562.5。 10)车环槽。 11)划12个φ33螺栓孔的线,并钻孔。 12)车外圆及孔口倒角。 13)按图纸要求检验。 5.5 筒节的制造 1.矫正 原理如图5.5所示。 图5.5 七辊矫平机矫正原理 2.划线 划线前应展开,可采用计算展开法。具体展开公式如下: L=π(Dg+δ)+S 式中 L---筒节毛坯展开长度(mm) Dg---容器公称直径(mm) δ---容器壁厚(mm) S---加
17、工余量(包括切割余量、刨边余量和焊接收缩量等)(mm),如两侧均需刨边,则取10~15mm。 筒体展开后,其实就是一块矩形金属板。毛坯宽度为筒节的长度,其大小取决于原材料的宽度和容器上焊缝的分布情况(焊缝不允许十字交叉)。注意,毛坯实际宽度也要包括加工余量S。 经查阅资料及计算,取划线尺寸为44572500(长度宽度)。 3.下料 采用等离子切割下料。 4.边缘加工 采用刨边机进行钢板的直线边缘加工和开坡口,加工精度高,坡口尺寸准确。 5.卷制 采用对称式三辊卷板机来卷制钢板。 (1)预弯 采用对称式三辊卷板机弯卷钢板时,钢板两端各有一平直段无法弯卷。为使钢板都能弯曲成同
18、一曲率,在卷板前要先将其两端弯曲成所需要的曲率,称为预弯。 本次设计利用压力机预弯。受模具长度限制,板料的压弯需逐段进行,且在压制过程中需要随时用样板检查曲率半径的大小,以保证成形尺寸满足要求。如图5.6所示。 图5.6 压力机预弯示意图 (2)对中 板料预弯后,放入卷板机上下辊之间进行辊卷前必须使板料的母材与辊的轴线平行,使板料的纵向中心线与辊的轴线保持相互垂直,即对中,其目的是防止钢板在滚卷过程中产生扭斜变形。 (3)卷圆 钢板对中后,即可用上辊压住板料并使之产生一定弯曲,开动机床进行滚卷。 每滚卷一次行程,
19、便适当下调上辊一次,这样经过多次滚卷就可将板料弯曲成所要求的曲率。在滚卷过程中要注意:随时用卡样板测量,看是否达到曲率要求,不可过卷量太多,因为过卷要比曲率不足难以修正,且易使金属性能变坏。在冷卷时要考虑到回弹的影响,必须施加一定的过卷量。当卷制达到曲率要求时,还应在此曲率下多卷几次,以使其变形均匀和释放内应力,减少回弹。如图5.7所示。 图5.7 滚卷示意图 6.对齐 用容器拉紧器使筒体要焊接的两边对齐。通过调节拉紧器上的横向螺母来保证焊接间隙筒,通过调节拉紧器上的径向螺母来消除焊缝错边。如图5.8所示。调节完毕后,把筒体放到焊接工作台
20、上进行焊接。 图5.8 拉紧器示意图 7.焊接 筒节采用复合钢板制造,外层先采用熔化极气体保护焊进行定位焊,然后正式施焊;内层采用手工堆焊。坡口形状及尺寸见图5.9。 图5.9 坡口形状及尺寸 熔化极气体保护焊采用H08CrMoC(φ1.0mm)焊丝,采用NB-200焊机, 工艺参数见表5.1。 表5.1 熔化极气体保护焊工艺参数 焊接电流/A 焊接电压/V 焊接速度/(m/h) 保护气体 保护气流量/Lmin-1 100~120 28~30 25 Ar(99.5%) 20 焊前150℃预热,焊后应进行650~830℃退火处理。 手工
21、堆焊采用ZXG-300硅整流式电焊机,堆焊工艺参数见表5.2。 表5.2 手工堆焊工艺参数 堆焊层 焊条牌号 规格/mm 焊接电流 /A 焊接电压/V 过渡层 309L Φ1.0 700-720 32-34 面层 347 Φ1.0 700-720 32-34 堆焊完成后缓冷。 8.矫圆 焊接结束后,在卷板机上进行矫圆,大致可分三个步骤。 (1)工件放入卷板机上辊之后,根据计算,将上辊调至所需要的最大矫正曲率的位置进行加载。 (2)使工件在矫正曲率下多次滚卷,并着重于焊缝区的矫正,使圆筒曲率均匀一致。经测量,直到合乎要求为止。 (3)逐渐卸除载荷,并
22、使工件在逐渐卸除载荷的过程中多次滚卷。 9.检验 按图纸要求检查尺寸等。 5.6 90度弯头的制造 弯头形状及尺寸见图5.10。 图5.10 弯头简图 1、零件的主要技术要求 1)表面不得有裂纹及其它降低弯头强度和连接可靠性的缺陷。 2)工件材料为0Cr18Ni10Ti。 2、工艺分析 根据工件材料性质和具体尺寸精度、粗糙度的要求,可以采用粗车的工艺来达到。 3、工艺过程 1)备φ27312(外径管厚)的管料。 2)采用弯压的方法,弯出90度弯头。 3)按图中所示尺寸加工成型。 4)车内、外圆倒角。 5)按
23、图纸要求检验。 5.7 接管的制造 接管形状及尺寸见图5.11。 图5.11 接管简图 1、零件的主要技术要求 1)表面不得有裂纹及其它降低弯头强度和连接可靠性的缺陷。 2)工件材料为0Cr18Ni10Ti。 2、工艺分析 根据工件材料性质和具体尺寸精度、粗糙度的要求,可以采用粗车的工艺来达到。 3、工艺过程 1)备φ32512的(外径管厚)的管料。 2)划线,满足长度667。 3)切割。 4)修整毛边。 5)按图纸要求检验。 5.8 锥体的制造 锥体形状及尺寸见图5.12。 图5.12 锥体简图 1、零件的主要技术要求 1
24、)表面不得有裂纹及其它降低锥体强度和连接可靠性的缺陷。 2)工件材料为0Cr18Ni10Ti。 2、工艺分析 根据工件材料性质和具体尺寸精度、粗糙度的要求,可以采用粗加工的工艺来达到。 3、基准选择 焊接时为避免错边,待焊的两边缘互为基准。 4、工艺过程 1)备厚度6mm的板料。 2)采用普通的三滚卷板机按图示尺寸卷制,做个可以转动的轴防止大小头向一个方向跑。 3)修整毛边。 4)焊接纵缝。 5)按图纸要求检验。 5.9 裙座基础板的制造 裙座基础板形状及尺寸见图5.13。 图5.13 裙座基础板简图 1、零件的主要技术要求 1)裙座螺
25、栓孔中心圆直径允差以及相邻两孔和任意两孔弦长允差均为2mm.。 2)工件材料为Q235-A。 2、工艺分析 根据工件材料性质和具体尺寸精度、粗糙度的要求,可以采用气割的工艺来达到。 3、基准选择 划边缘12个豁口以圆心和水平虚线为定位基准,划内径的线以圆心为基准。 4、工艺过程 1)选厚度20的钢板,采用气割落φ1604的圆板料。 2)打磨毛边。 3)划出内径和12个边缘豁口的线。 4) 气割割出内径和豁口并打磨毛边。 5)按图纸要求检验。 5.10 接头的制造 接头形状及尺寸见图5.14。 图5.14 接头简图 1、零件的主要技术
26、要求 1)表面不得有裂纹及其它降低接头强度和连接可靠性的缺陷。 2)工件材料为15CrMo,锻件,级别III。 2、工艺分析 根据工件材料性质和具体尺寸精度、粗糙度的要求,可以采用粗车的工艺来达到。 3、基准选择 以较粗一端的端面为定位基准。 4、工艺过程 1)采用GB4235锯床,从φ250mm的圆钢上锯取长462mm的一段。 2)始锻温度1150~1200℃,终锻温度800~850℃,使直径达φ3282mm,厚度达2762mm。 3)滚圆修整。 4)用凸模冲出φ260的通孔。 5)热处理,650~830℃退火,恢复组织。 6)粗车一端外圆和端面至φ32
27、6274。 7)钻中心孔至φ50,镗中心孔至φ260。 8)车外圆及孔口倒角。 9)倒头粗车另一端外圆和端面至φ325273。 10)按要求粗车车出的斜椎式外圆。 11)车外圆及孔口倒角。 12)按图纸要求检验。 5.11 其它零件的制造 筋板、盖板、垫板这些零件都是一些板料。按照尺寸划线,留出加工余量3~5㎜,用气割法切割。机加工表面去除四周毛刺,并用砂纸打磨表面,去除表面氧化物、油渍等,以便后面焊接。 6 主要部件的制造 6.1 筒体 装配简图及系统图见图6.1。 (a) (
28、b) 图6.1 筒体装配简图及系统图 以筒节16-4为基准件,采用卧装,装配时需要借助于装配胎架,筒体在滚轮架和辊筒架上装配。对接装配时,将两圆筒置于胎架上靠紧或按要求留出间隙,然后采用测量圆筒同轴度的方法,校正两节圆筒的同轴度,校正合格后施行定位焊。 其焊接工艺完全参考前述5.5中筒节纵缝焊接工艺。 6.2 筒体与封头 装配简图及系统图见图6.2。 (a) (b) 图6.2 封头与筒体装配简图及系统图 以筒体为基准件,采用吊装,按图所示依次装配、点固,保证各零件的中心线如图中所示,从而完成装配。 其焊
29、接工艺完全参考前述5.5中筒节纵缝焊接工艺。 6.3 法兰与法兰盖 法兰与法兰盖装配见图及系统图见图6.3。 (a) (b) 图6.3 法兰与法兰盖装配简图及系统图 以法兰盖为基准件,按图所示装配、点固,保证各零件的中心线如图中所示,从而完成装配。 坡口形式及尺寸如图6.4。 图6.4 坡口形状及尺寸 采用熔化极气体保护焊,采用H08CrMoC焊丝,采用NB-200焊机。 焊前用钢丝刷清理坡口及附近杂质。 焊前预热温度为150℃,焊接工艺参数如表6.1。 表6.1 TIG焊工艺参数 焊材规格
30、 /mm 焊接 电流/A 保护 气体 电弧电压/V 保护气流量/L.min.-1 Φ1.2 110~130 Ar(99.9%) 12~14 15 焊后650~830℃退火处理。 其焊接工艺参见附录B。 然后对部件内壁和密封面进行堆焊,采用带极堆焊,焊机型号ZDE-1250,焊接工艺参数见表6.2。 表6.2 带极堆焊工艺参数 层次 焊带+焊剂 规格(mm) 电流(A) 电压(V) 焊速(cm/min) 过渡层 D309L+SMJ34 0.450 700-720 34-36 12-15 表面层 D347+SMJ34 0.4
31、50 700-720 34-36 12-15 6.4 出口弯管 出口弯管装配简图及系统图见图6.5。 (a) (b) (c) 图6.5 出口弯管装配简图及系统图 先以法兰为基准件,将法兰和接管装焊为套件。 再以弯头为基准件,采用V型槽和很短的V型槽定位,然后采用V型槽定位接头,接着再采用V型槽定位法兰、接管组成的套件,夹紧后定位焊。具体采用的夹具见后叙的出口弯管工装夹具设计。 其装配工艺参见附录C。 图6.5(a)中I和III焊缝为异种钢(耐热钢与奥氏体不锈钢)之间的焊缝,采用手工电弧焊,焊条牌号A042,焊前焊条须经200-250℃烘焙1h,用
32、ZXG-300硅整流式电焊机。坡口形式及尺寸见图6.6,焊前用钢丝刷清除坡口两侧50mm内的油污、铁锈、氧化皮等杂质,并用丙酮清洗。焊接工艺参数见表6.3。 图6.6 坡口形状及尺寸 表6.3 手工电弧焊工艺参数 焊接电流/A 焊接电压/V 焊接速度/(m/h) 230~250 28~30 20~25 图6.5(a)中II焊缝采用熔化极气体保护焊,采用NB-200焊机,采用H0Cr19Ni9Ti焊丝,保护气体为Ar(99.9%),坡口形式及尺寸见图6.6,焊前用钢丝刷清除坡口两侧50mm内的油污、铁锈、氧化皮等杂质,并用丙酮清洗。焊接工艺参数见表6.4。 表6.4
33、 熔化极气体保护焊工艺参数 焊丝直径/mm 焊接电流/A 焊接电压/V 焊接速度/mm.min.1 保护气流量/L.min.-1 1.2 180~200 24~26 300 15 6.5 分配锥 分配锥装配简图及系统图见图6.7。 (a) (b) 图6.7 分配锥装配简图及系统图 以孔板为基准件,按图所示依次装配、点固,保证各零件的中心线如图中所示,从而完成装配。 采用手工电弧焊,焊条牌号A137,采用ZXG-300硅整流式电焊机,焊接工艺参数见表6.5。 表6.5 手工电弧焊工艺参
34、数 焊接电流/A 焊接电压/V 焊条直径/(mm) 160~180 16~18 3.2 坡口形式及尺寸如图6.8。 图6.8 坡口形式及尺寸简图 焊后打磨焊缝表面。 6.6 裙座底部 裙座底部装配图及系统图见图6.9。 (a) (b) (c) 图6.9 裙座底部装配简图及系统图 以基础板为基准件,按图所示依次装配、点固,如图中所示,从而完成装配。 采用手工电弧焊,焊条牌号E4303,采用ZXG-300硅整流式电焊机,焊接工参数见表6.6。 表6.6 手工电弧焊工艺
35、参数 焊接电流/A 焊接电压/V 焊接速度/(mm/min) 160~180 20~22 220 7 总装配 整体上讲采用吊装。 1.预先将裙式支座,通过地脚螺栓固定在地面上,然后将下封头吊起,与裙座按装配图所示进行装配,并焊接固定。 2.用吊车将壳程吊起,按装配图所示进行装配,并焊接固定。 3. 用吊车将上封头组吊起,按装配图所示进行装配,并焊接固定。 至此,加氢反应器总装完毕。 8 出口弯管工装夹具设计 8.1 夹具设计任务 焊接产品“出口弯管”的产品图见图6.5(a)。 出口弯管由接头、弯头、接管、法兰构成;接头和法兰材料为15CrMo,弯头
36、和接管材料为0Cr18Ni10Ti;出口弯管的总体尺寸是(长宽高)1362.5510909。 焊接产品“出口弯管”的技术要求分析: (1)件3与件4中心线之间重合,件1和件3的中心线与件2中心线的切 线重合。 (2)接头中心线与右端面距离12001.0。 (3)法兰中心线与上端面6541.0。 8.2 工件的定位及夹紧原理 以弯头为基准件。弯头是由较长的90度V型槽和很短90度V型槽定位的,基准面是槽面。接头是由V型槽配合基准件定位的,接管和法兰组成的套件也是采用V型槽配合基准件定位的。 扭动手柄使螺杆带动压板向下移动,压住零件。 8.3 主要零件设计说明 底座:固定弯
37、头支承座、接头支承座、接管支承座、升降架,减小整个夹具对地面的压强。 弯头支承座:放置弯头,并对弯头定位。 接头支承座:放置接头,并对接头定位。 接管支承座:放置接管,并对接管定位。 夹紧器支架:与手柄、螺杆、压板配合夹紧零件。 8.4 夹具使用说明 1)拧动手柄,使螺杆带动压板向上移动。 2) 把弯头放入弯头支撑座上,拧动手柄夹紧。 3) 把接头放入接头支撑座上,移动接头,使接头与弯头边相距2~3mm,拧动手柄夹紧接头。 4) 把接管与法兰组成的套件放入支撑座上,移动套件,使接管与弯头边相距2~3mm,拧动手柄夹紧套件。 5) 焊接。 6) 拧动手柄,取出焊件。 9
38、 检验 容器全部受压焊缝进行100%X射线探伤检查,射线探伤符合JB/T 4730.2-2005《承压设备射线检测》规定中Ⅱ级合格。设备制造完毕后,以2MPa进行水压试验,合格后再以1.8MPa进行气密性试验,检验过程如下。 9.1 表面检查 表面检验是检查产品表面是否有大的缺陷,主要进行的是焊接坡口、焊缝余高、焊缝表面质量检验等。具体要求为:①焊接坡口:不得有裂纹、分层、夹渣等;②焊缝余高:余高0~2.5mm③焊缝表面质量:不得有裂纹、气孔、弧坑、夹渣、熔渣、未融合、飞溅物。 9.2 X射线探伤 原理:利用X射线可穿透物质和在物质中有衰减的特性来发现缺陷。它适用于检查弓箭内部
39、的缺陷。对气孔、夹渣等体积性缺陷,具有较高的检测灵敏度。 焊缝射线探伤的一般程序:焊缝表面质量检查→核对实物与委托单项目→机器预热画草图→贴片、贴标、屏蔽散射线→对位选焦距→开机透照→胶片处理→底片评定→签发检验报告→底片及资料存档。 9.3 水压试验及要点 水压试验的水温≥30℃,采用水泵加压试验。用水泵将容器充满水,堵住容器上的一切孔。试验时,升压或降压均应缓慢进行。当升至工作压力时暂停,进行初检,无异常可继续升压到规定压力进行保压,然后降至工作压力或设计压力,保持30min进行仔细检查。试验压力为工作压力的1.5倍,即2.25Mpa。加压后距离焊缝20mm,用小锤轻轻锤击,然后卸
40、载。 结果分析与判定:保压时,表压稳定准确;检查所有焊缝部位,无渗水或水珠;肉眼观察没有发现残余变形,焊缝强度为合格。 9.4 气密性试验及要点 气密性试验比水压试验灵敏、迅速,试验后不用排水处理,按照设计规定,进行P=0.392MPa的气密性试验。所用气体必须干燥洁净,气温不得低于15℃,当试验压力达到规定值时,停止加压。施压下的产品不得敲击、振动和修补缺陷焊缝。 结果分析与判定:停止加压后,用涂肥皂水检漏或检查工作压力表的数值变化。肉眼观察未发现残余变形,如没有发现漏气或压力表数值不稳定,则焊缝强度为合格。 10 结束语 本文在分析加氢反应器结构的基础上,对加氢反应器的生产
41、步骤进行了方案分析,并与实际密切结合,确定了加氢反应器的生产工艺。重点阐述法兰盖、封头等零件的加工工艺,出口弯管、法兰与法兰盖等部件的装焊工艺,并根据加氢反应器制造的需要,设计了出口弯管焊接工装夹具。 本次设计的加氢反应器各结构件的制造、焊接方法等均符合《加氢反应器制造技术要求》及《焊接手册》的有关要求和规定。焊缝经过X射线探伤可保证焊缝的质量要求。经过水压试验和气密性试验可以初步保证应用水平,但是否具备合格的使用条件还需根据成品在服役期间的工作情况来判定。
42、 参考文献 [1] 张振戎, 卢庆春. 加氢反应器的发展历史 [ J ] .一重技术, 2004:122~125. [2] 李超. 国内外加氢技术特点及发展趋势 [ J ]. 石油规划设计, 2004, 5 (6) : 5~8. [3] 袁耀如. 加氢反应器制造与使用中的问题及对策 [ J ]. 石油化工设备, 2004, 33 (2) : 70 - 72. [4] 李波, 郑启文. 加氢反应器损伤及检验技术探讨[ J ]. 化工科技, 2004, 12 (5) : 39
43、- 42. [5] 孟庆森,吴志先.金属材料焊接基础.北京:化学工业出版社.2006,3: 85~130. [6] 李亚江,王娟.耐热钢焊接及工程应用.北京:化学工业出版社.2003,9:160~190. [7] 王国凡.钢结构焊接制造.北京:化学工业出版社.2004,5:100~160. [8] 李淑华,王申.焊接工程组织管理与先进材料焊接.北京:国防工业出版社.2005,5:11~12,99~100. [9] J.F.Lancaster,THE Physics of Welding NEW YORK: PERGAMON PRESS,1984 [10] H.Sekig
44、uchi.Fundamental Research on the Welding Heat-affected Zone of Steel.The Nikkan Kogyo Shimbun Ltd.1976. [11] 邓文英,宋力宏.金属工艺学.北京:高等教育出版社.2008, 35(4) : 5~105. [12] 王先奎.机械制造工艺学.北京:机械工业出版社. 2007,3: 5~30. [13] ASME.Boiler and Pressure Vessel Code Welding and Brazing Qualification Section IX. 2004:32
45、. [14] 周浩森.焊接结构生产及装备.北京:机械工业出版社.1998,5:132~145. [15] 李亚江.焊接材料的选用.北京:化学工业出版社.2004,3:95~124. [16] 黄蓝林.焊接生产工艺设计.西安:西安交通大学焊接研究室,2005:3~6. [17] 李亚江,刘强,王娟.焊接质量控制与检验.北京:化学工业出版社,2006,6: 123~125. [18] N.Yurioka.Determination of Necessary preheating Temperature in steel Welding.Welding Journal.1983
46、,62(6):147~152. [19] 董大勤.压力容器设计手册.北京:工业出版社.2006,1:289~295. [20] 史光远.焊接结构设计与制造.黄河水利出版社,2006,10:53~60. [21] 陈焕明.焊接工装设计.北京:航空工业出版社.2006,8:251~269. [22] 韩广利,曹文杰.机械加工工艺基础.天津:天津大学出版社.2005,9:35~69. [23] 梁启涵.焊接检验.北京:机械工业出版社.2004,1:740~760. [24] 强天鹏.压力容器检验.北京:新华出版社.2008,9:85~87.
47、 致 谢 此次毕业设计从二零一 一年三月下旬开始,到六月中旬结束,历时三个月左右的时间。我的导师给了我很多的理论指导,使我在短短三个月的时间里学到了很多东西,同时我也从老师的身上体会到一个科学工作者对学问一丝不苟的严谨态度,也更深一步体会到这种严谨的科学态度对研究学问的重要性。正是有了老师的耐心指导和严格要求,我才能够顺利地完成本次设计。 在设计过程中, 等同学也给我提出不少宝贵意见,并在我感觉设计没有头绪时,给我找了不少参考书,使我对课题有了进一步认识。在此一并表示感谢。 最后,再次衷心地感谢老师和其他给过我帮助的老师和同学! 第 35 页 共 35 页
- 温馨提示:
1: 本站所有资源如无特殊说明,都需要本地电脑安装OFFICE2007和PDF阅读器。图纸软件为CAD,CAXA,PROE,UG,SolidWorks等.压缩文件请下载最新的WinRAR软件解压。
2: 本站的文档不包含任何第三方提供的附件图纸等,如果需要附件,请联系上传者。文件的所有权益归上传用户所有。
3.本站RAR压缩包中若带图纸,网页内容里面会有图纸预览,若没有图纸预览就没有图纸。
4. 未经权益所有人同意不得将文件中的内容挪作商业或盈利用途。
5. 装配图网仅提供信息存储空间,仅对用户上传内容的表现方式做保护处理,对用户上传分享的文档内容本身不做任何修改或编辑,并不能对任何下载内容负责。
6. 下载文件中如有侵权或不适当内容,请与我们联系,我们立即纠正。
7. 本站不保证下载资源的准确性、安全性和完整性, 同时也不承担用户因使用这些下载资源对自己和他人造成任何形式的伤害或损失。